Homogeneous characteristics //
Before getting to the specifics of each material, there are a couple of issues that apply to all materials. First, it is important that the insulating material is homogeneous. This is to ensure that the dielectric constant is the same throughout so that the electric field strength gradient is as constant as practical.
Also, if there are any air pockets, there could be corona or localized arcing. The implications range from rapid insulation failure, to gradual, long term degradation. Thus, it’s a good idea to include a method for removing air from any encapsulant.
One implication of homogeneity is that it is generally not a good idea to use more than one insulation material. Putting two materials “in series” can do more harm than good.
Second, it is important to derate the insulation’s dielectric strength, often expressed in volts per mil. The amount of derating depends upon the shapes of the conductors (the “sharp points” issue), the insulator thickness, and the insulator homogeneity.
Generally, you derate the dielectric strength as the material gets thicker. For many materials you can find an equation that describes the relationship between thickness and dielectric strength.
Insulation materials
Here are 7 most common and known materials used in electronics assemblies as high voltage insulation, and descriptions of issues that require special attention.
1. Air

It’s free and the cost is certainly a big advantage of air. However, air has the worst dielectric strength of all the insulators in this listing, so distances will need to be the greatest for a given geometry.
A second consideration is that surfaces need remain clean and free of dust over long periods, so that there is no arcing along a surface.
2. Sulphur Hexafluoride (SF6)
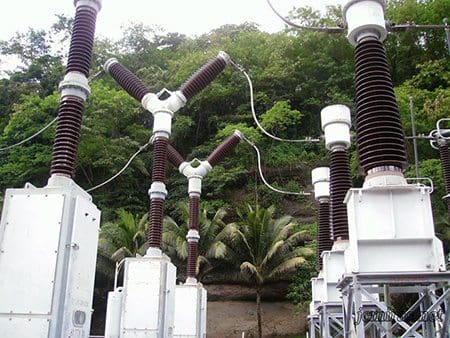
This is a great insulator in that parts remain clean, and assemblies are easy to work on once the housing is opened and the gas is replaced by air. One difficulty with using SF6 is that the housing must be hermetically sealed. Two safety issues exist. Poisonous gasses are formed whenever there are arcs.
Also, it is extremely hazardous if someone breathes in any SF6. It is denser than air, and will settle in the bottom of one’s lungs, and suffocation can result. Since it is a colorless, odorless gas, it goes undetected. Extreme care must be taken to avoid inhalation.
Interesting reading: Are Your Circuit Breakers Healthy?
3. Epoxy

While epoxy has good thermal characteristics and excellent adhesion, if not used properly during the manufacturing process, it can ruin components in a high voltage assembly. Stresses during the potting process can damage components.
Thermal stresses during equipment operation can also damage components due to unequal thermal expansion and contraction. In addition, the epoxy curing process can be highly exothermic and parts can be damaged by heat generated during curing.
Epoxy modules are unrepairable, so if there is a failure, the assembly must be discarded.
The other implication is that failure analyses are severely limited, making it difficult to learn from any problems that crop up.
4. Two-part Silicone (Two-Part)
Like epoxy, silicone encapsulation is in widespread use in the high voltage industry. Poor adhesion is perhaps the biggest shortcoming of silicones. However, preparing the surface properly can alleviate this. Some silicones are adversely affected by certain materials. In the presence of these materials, the curing process is inhibited, and the silicone never cures.
In addition, most silicones do not have good thermal conductivity, as compared to most epoxies.
5. One-part Silicone
One part silicones are available in “self leveling” and thixotropic form. Thixotropic materials do not flow and remain in whatever shape they emerge in from the tube. It is somewhat like shaving cream in that respect. Prior to curing, the thixotropic silicone can be formed into a desired shape. Air bubbles can be trapped in cured thixotropic silicones, and thus their use is limited.
One more thing to watch for is that some one-part silicones will corrode electronic assemblies.
6. Oil
Oil is in widespread use in part due to its relatively low cost and thermal characteristics.
Prior to 1977, some oils were dangerous due to the inclusion of toxic PCB’s (polychlorinated biphenyls), but this is thankfully an issue of the distant past. Considerations include the need to have a sealed housing with a provision for expansion and contraction.
Oil can easily become contaminated by arcing and with the buildup of foreign materials. In addition, it can be messy to work with oil.

7. Perfluorinated Liquids
One trade name of perfluorinated liquids is FluorinertTM. They are clear, colorless, odorless and have a viscosity similar to water. Concerns include the need to have a sealed housing with a provision for expansion and contraction. It is expensive, and evaporation is an issue.
In some cases, evaporation is so fast you can almost see dollar bills disappearing into thin air!
No comments:
Post a Comment