
PLC programs are never final…
Yes, PLC programs are never final, it is always possible to make corrections and subsequent adaptations to new system according the customer requirements. Even during commissioning,program changes are often necessary. The commissioning of a system can be divided into four steps:
- Checking the hardware
- Transferring and testing the software
- Optimization of the software
- Commissioning of the entire system
1. Checking the hardware
Each sensor, switch and button is connected to a specific input and each actuator to an output. During engineering process addresses and wires must not be mixed up. Also, the sensors and actuator placing should be checked (that they are where they have to be in the automated system).
During checking procedure, the outputs are set in a test mode. The actuators must then meet the specified requirements (functions). If changes are made, then the documentation (allocation list, drawings, etc) must also be updated to respond to reality.
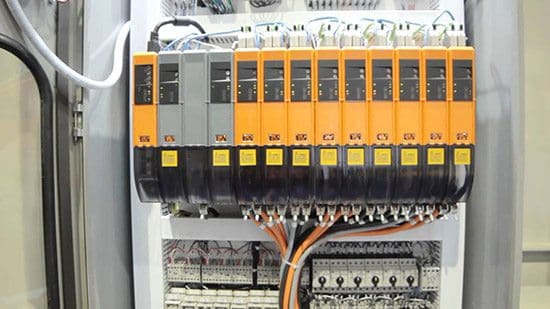
1.1 Testing inputs and outputs
Input devices, e.g. switches, can be manipulated to give the open and closed contact conditions and the corresponding LED on the input module observed. It should be illuminated when the input is closed and not illuminated when it is open.
Failure of an LED to illuminate could be because the input device is not correctly operating, there are incorrect wiring connections to the input module, the input device is not correctly powered or the LED or input module is defective. For output devices that can be safely started, push buttons might have been installed so that each output can be tested.
2. Transferring and testing of software
Prior to commissioning, all available off-line and virtual PLC program testing tools should be used intensively to find program faults. For example, such test tool is in STEP 7 as subprogram S7-PLCSIM. It simulates the work of a PLC (virtual PLC) and allows the user written PLC program to be tested.
Following this, the program is transferred to a central processing unit in the virtual PLC. The entire program is executed without using the real PLC.
The user has to simulate the input signal changes and verify how the outputs react to it. Some PLCs offer simulation in a real PLC: the entire program is executed in a PLC without the real inputs and outputs being connected. Processing of the PLC outputs thus only takes place in the PLC image table. The physical PLC I/Os are not updated to/from the PLC I/O images.
Therefore this eliminates the risk of damaging machines or system parts.
After this, the individual user program parts and system functions are tested: manual operation, setting, individual monitoring programs etc. and finally the interaction of the program parts with the help of the main program.
The system can and should be commissioned step-by-step. Important aspects of commissioning and fault detection are the test functions of the programming system, such as the single-step mode or the setting of stop points. The single-step mode in particular is of importance, whereby theprogram in the PLC memory is executed line-by-line or step-by-step. In this way, any program faults which may occur in the program can be immediately localized.
3. Optimization of the software
User programs can almost always be improved after the first test run. It is important that any corrections or modifications are made not just in the PLC user program, but are also taken into account in the documentation.
4. Commissioning of the entire system
This already occurs in part during the testing and optimization phase. Once the final status of thePLC user program and the documentation is established, all the controller functions (in accordance with the automation task) need to be executed step-by-step again.
If no faults occur by the entire system commissioning, then the system is ready to be handed over to the customer.

References //
- Application of PLC industrial automation – AutoMatic
- Programmable Logic Controllers by W. Bolton
No comments:
Post a Comment